Latest videos
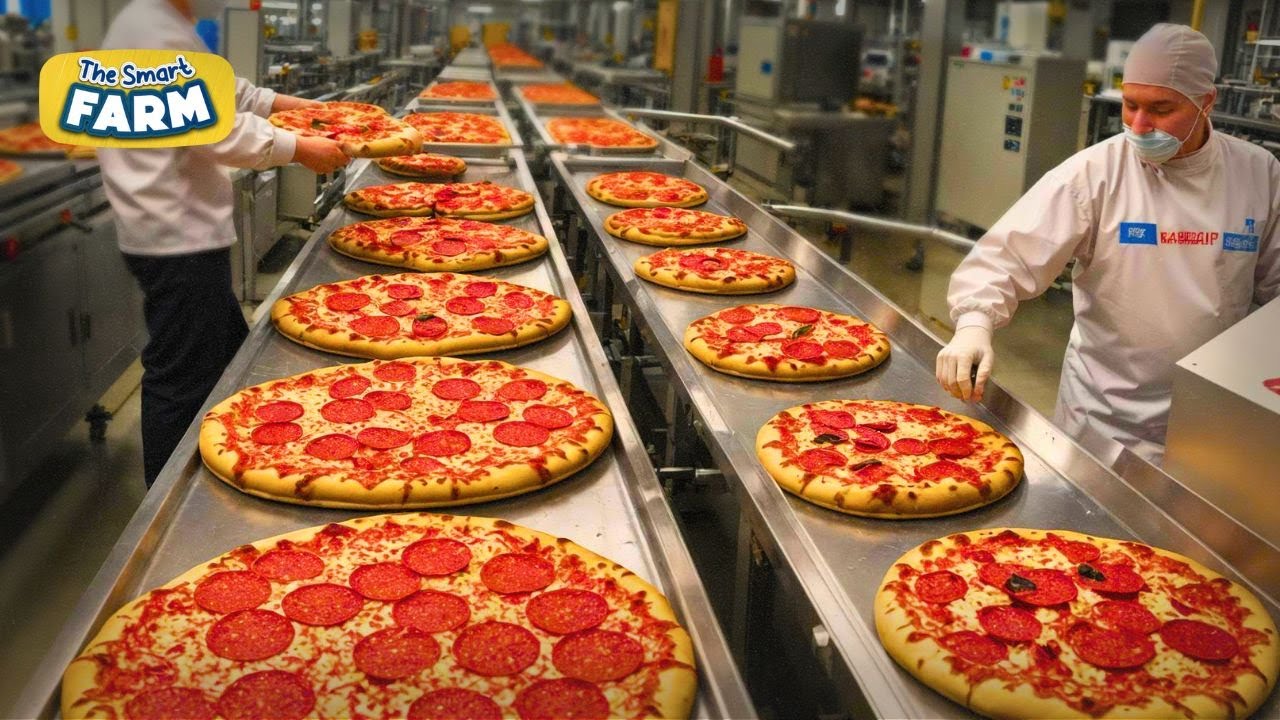
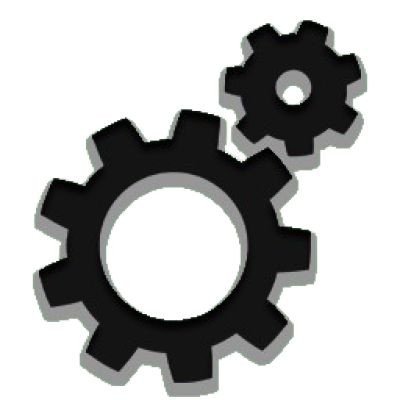
Making frozen pizzas for mass distribution involves a series of automated steps: Large mixers combining flour, water, yeast, and other ingredients create a smooth dough in large quantities.
The dough is then automatically divided into portions which are transported on long conveyor belts to sheeting machines, which flatten and shape them into precise, circular bases suitable for various pizza sizes.
Automated sauce applicators evenly spread tomato sauce on the dough, adjusting quantities based on pizza size. Toppings are added through automated systems, ensuring even distribution of cheese, pepperoni, vegetables, and other ingredients.
The pizzas then enter large ovens, operating at precise temperatures, to achieve a crispy crust, melt the cheese, and cook the toppings. After baking, the pizzas cool down on conveyor belts, passing through freezers and inspection stations equipped with cameras and sensors to ensure quality. Packaging stations are also where machines place them in cardboard boxes or plastic wraps, sealing in freshness.
The reported increase in U.S. sales of frozen pizza from approximately 6.06 billion U.S. dollars to 6.77 billion U.S. dollars between 2021 and 2022 underscores the growing popularity and demand for this convenient food option. Several factors could contribute to this upward trend. Firstly, the convenience and ease of preparation associated with frozen pizzas make them an attractive choice for consumers with busy lifestyles, especially amid the ongoing challenges posed by the COVID-19 pandemic.
This is The Smart Farm! A heavenly space featuring harvesting innovation and production line insights.
🟡 SUBSCRIBE to THIS channel ➤ https://www.bit.ly/3N8x9Ie
🟡 LIKE the video for support!
You can support the companies featured in this episode:
AMF Bakery Systems
https://amfbakery.com/
Memak Bakery
https://www.memak.com/en/anasayfa.html
Emilia Foods
https://www.emiliafoods.com/
Gottlieb bakery
https://www.pack.co.il/
Trak Makine
https://trakmakine.com/
Tekpak Automation Ltd
https://tekpakautomation.com/
Integrated Bakery BV
https://integratedbakery.com/
DIENST Packsystems
https://www.dienst-packsystems.de/
Texwrap
https://www.texwrap.com/
Rademaker BV
https://www.rademaker.com/
Grote Company
https://www.grotecompany.com/en-us/
If you are the owner or if you want to be featured please contact us at thesmartfarm@yahoo.com
We will follow your request as soon as we receive your message.
Copyright disclaimer section 107 of the Copyright Act 1976. "fair use" is allowed for purposes such as criticism, comment, news reporting, teaching, scholarships, and research.
We are not affiliated with the businesses whose products are shown in this documentary.
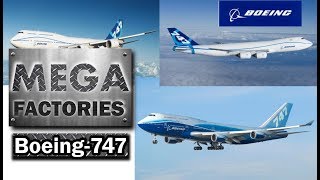
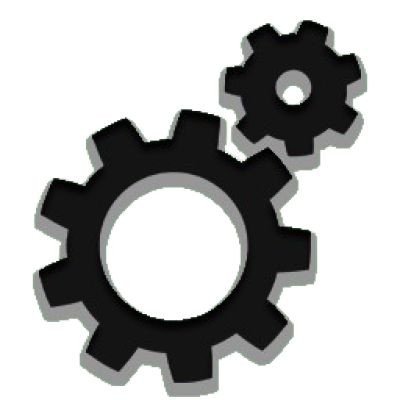
MEGAFACTORIES: Boeing 747 ||Audio in Hindi ||
The Boeing 747 is an American wide-body commercial jet airliner and cargo aircraft. The first wide-body airplane produced, it was the first plane dubbed a "Jumbo Jet". Its distinctive hump upper deck along the forward part of the aircraft has made it one of the most recognizable aircraft.
Manufactured by Boeing's Commercial Airplane unit in the United States, the 747 was originally planned to have 150 percent greater capacity than the Boeing 707,
The newest version of the aircraft, the 747-8, is in production and received certification in 2011. Deliveries of the 747-8F freighter version began in October 2011; deliveries of the 747-8I passenger version began in May 2012.
All Copyrights Are Reserved By National Geographic.
This Is National Geographic Property.
This video recorded from National Geographic.
For Educational Purpose.
To Know Megafactories.
Description Credit--https://en.wikipedia.org/wiki/Almarai
Fair Use Notice:
For educational purposes only.
#Boeing747#megafactories#jigyasa
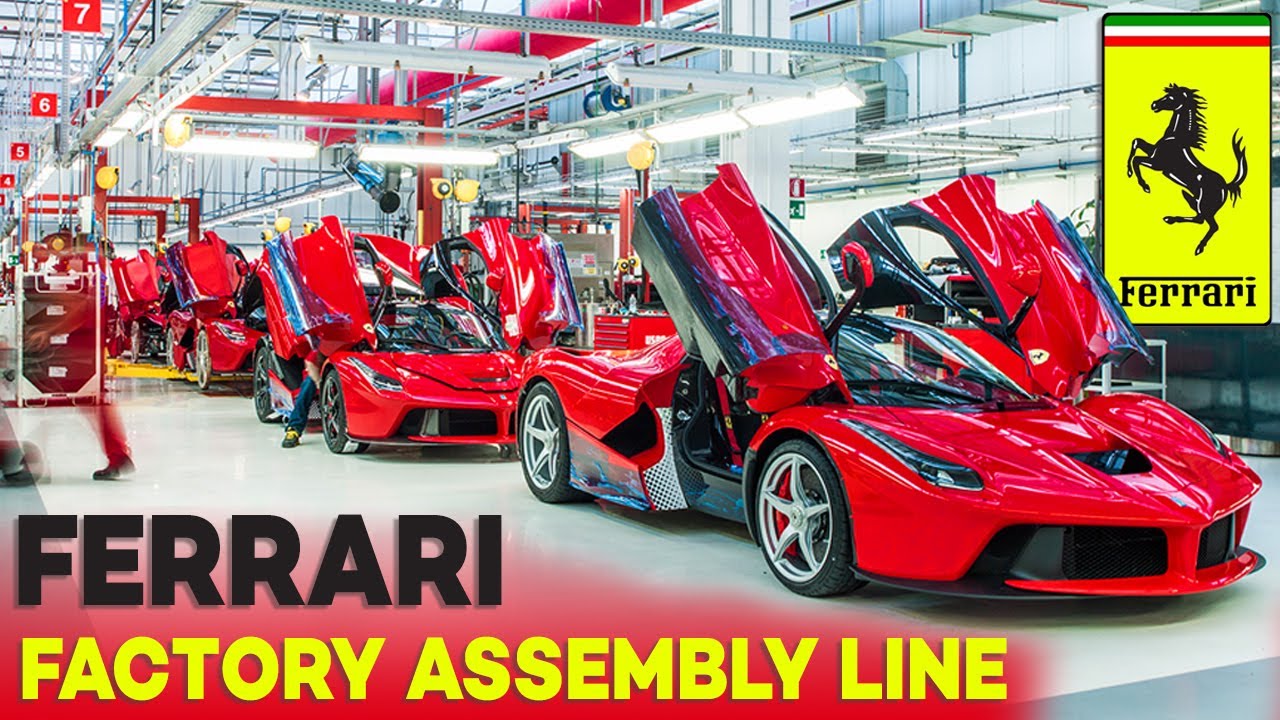
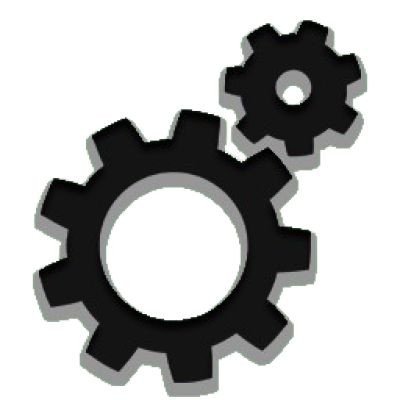
Ferrari Factory, Assembly manufacturing process, Production & Assembly Process- Inside the Factory (Ferrari Restarts Production, Maranello Italy) Making of Ferrari!ferrari assembly
Witness the birth of a Ferrari from. It is the world's most famous sports car Ferrari. Takes you inside Ferrari's factory in Maranello, Italy. Learn the design secrets of Ferraris newest car...
#Ferrari #supercar #Factory #Ferrarifactory #Assemblyline #MegaFactory #FactoryTour #SuperCar #SuperCarFactory #luxury #LuxuryLiving #ExplorerFerrari #LuxuryLiving #ferrari488 #Ferrari488 #ferrarilaferrari
Ferrari: https://www.ferrari.com/
🎵 Music: https://www.bensound.com/
Please send a message to me if you have any idea or copyright issues.
Contact: mesitech1@gmail.com
Thank for watching and reading.
Please Subscribe and share our videos!

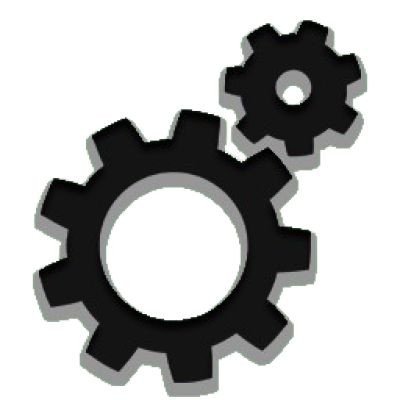
How do they make Kit kats? It is one of a short video in a series of short, concise videos that reveal the mysteries behind how everyday things happen.
Lays Factory: https://youtu.be/L6IYy95ODDU
Marshmallow Factory: https://youtu.be/tHxd5B4mbVc
Cadbury Dairy Milk Factory: https://youtu.be/tQhkbWRH9X0
Orange Juice Factory: https://youtu.be/VIMzn_obxgw
Food Factory Videos: https://bit.ly/FoodFactories
+-+-+-+-+-+-+-+-+-+-+-+-+-+-+-+-+-+-+-+-+-+-+-+-+-+-+-+-+-+-+-+-+-+-+
Timestamps
00:00 Intro
00:09 How Biscuits Are Made
00:58 How Kit Kats Are Made
04:30 How Ice Cream Is Made
SUBSCRIBE to THIS channel ➤ https://bit.ly/WondasticTech
And hit the LIKE button for support :-)
+-+-+-+-+-+-+-+-+-+-+-+-+-+-+-+-+-+-+-+-+-+-+-+-+-+-+-+-+-+-+-+-+-+-+
✪ Instagram: https://www.instagram.com/WondasticTECH
✪ Facebook: https://www.facebook.com/WondasticTECH
✪ Twitter: https://twitter.com/WondasticTECH
✪ Pinterest: https://www.pinterest.com/WondasticTECH
+-+-+-+-+-+-+-+-+-+-+-+-+-+-+-+-+-+-+-+-+-+-+-+-+-+-+-+-+-+-+-+-+-+-+
If you enjoyed, Please share with your friends.
Contact: contact@wondastictech.com
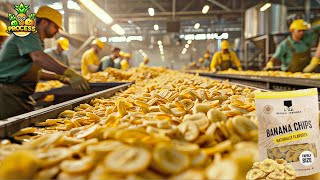
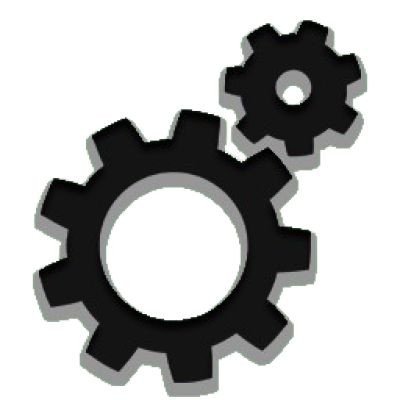
Ever wondered how your favourite banana chips are made? Join us as we take you inside our factory for an exclusive look at the entire banana chips production process. From fresh bananas to crunchy perfection, see how it's all done!
Video Segments:
Harvesting the Bananas
Quality Control
Peeling and Slicing
Frying
Seasoning
Packaging
Final Quality Check
More Videos:
** Link For Mcdonald’s Fries: https://youtu.be/y8KHgNZpMug
** Link For Coca-Cola: https://youtu.be/v8U2zKW2Nr8
Copyright Disclaimer: All rights reserved to the respective owners. The material in this video is not owned by this channel and is used either under license or under fair use guidelines.
Fairuse Disclaimer: This video is for educational and informational purposes only. It includes copyrighted materials that have not been specifically authorised by the copyright owner. We believe this constitutes a 'fair use' of any such copyrighted material as provided for in section 107 of the U.S. Copyright Act. Under Title 17 U.S.C. Section 107, the material in this video is distributed for educational, scholarly, and research purposes only.
Thumbnail images for this video were created using artificial intelligence. These images are conceptual and generated by AI based on the content themes discussed in our videos. They are artistic interpretations and not direct representations of actual events or visual depictions of factual content.
This video is not sponsored. All products and brands mentioned or shown in this video are not endorsed by, directly affiliated with, or sponsored by our channel.
----------------------------------------------------------------------------------
Welcome to Process Zone. We'll take you where cameras usually aren't allowed. Join us as we explore the fascinating world of manufacturing and discover the secrets behind some of the most popular products you use every day. Subscribe to Process Zone and get ready to be amazed by what you see!
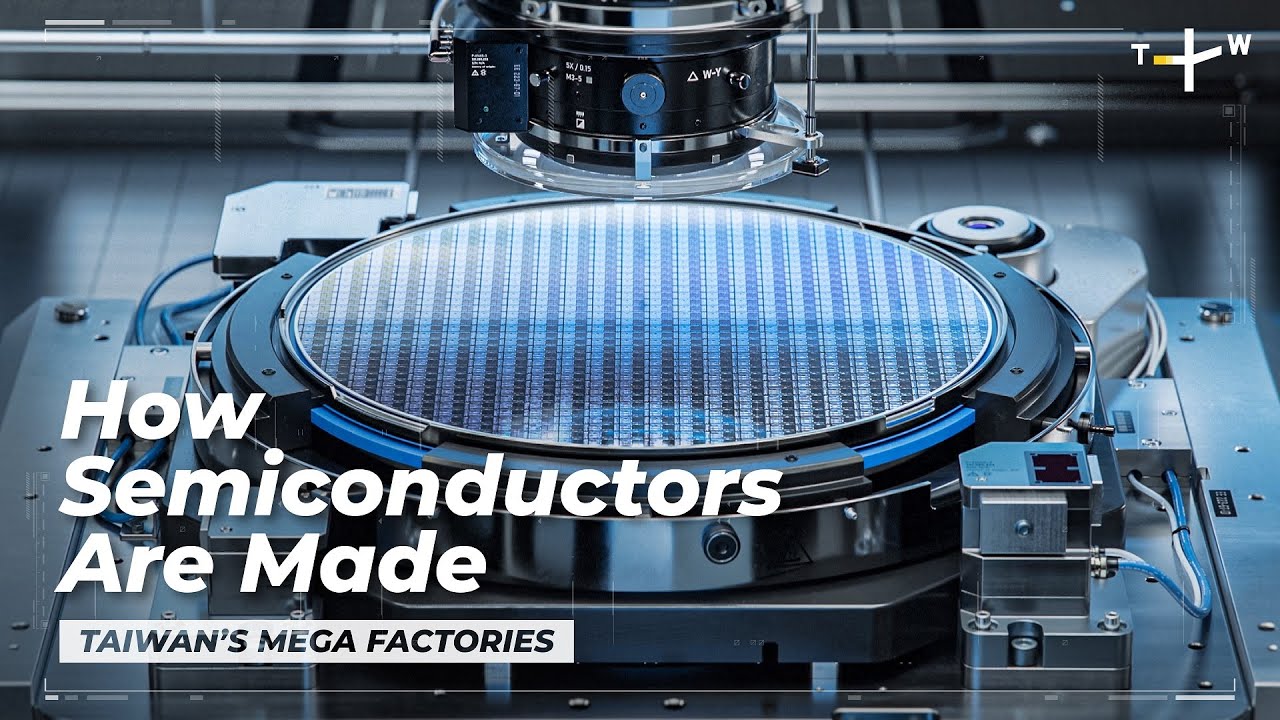
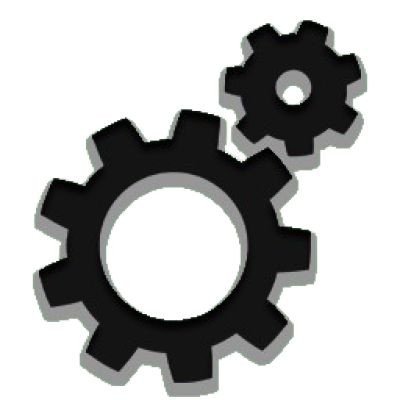
Join us for a tour of Micron Technology’s Taiwan chip manufacturing facilities to discover how chips are produced and how innovations in the semiconductor industry impact people and businesses all over the world.
Take a look inside one of the semiconductor factories that make Taiwan the most significant site of semiconductor production in the world. Thanks to modern technology and constant innovations, chip manufacturing advances at a rapid pace. Today, each silicon microchip contains over 100 billion transistors, the switches that make up the basic units of computing. Each transistor is just a few nanometers in size, making them a fraction of the size of a human hair.
This means that even the slightest contamination can halt the entire chip production process. In fact, the semiconductor manufacturing process contains over 1,000 steps, all of which must be executed perfectly to produce functional chips. In Micron’s mega factory, silicon wafers are processed with incredible precision. The dustless factory is highly automated, which minimizes the number of humans required to enter. Each silicon wafer is coated in a UV-sensitive liquid, then etched using photolithography. We exhibit the entire process here in high resolution, giving you an inside look into the workings of one of the most high-tech factories in the world.
Micron Technology is a global leader in the semiconductor industry and produces leading-edge memory products. Its neighbor Taiwan Semiconductor Manufacturing Company (TSMC) produces industry-leading logic technology. These two companies constitute a large portion of the Taiwanese semiconductor industry, which spans the island from north to south. As they grow and continue to innovate, their products require more and more resources to produce, putting increasing pressure on the environment. Micron leaders share how they are expanding their innovative approach into the area of resource management, enabling them to create more sustainable products.
Chapters:
00:00 Taiwan’s Semiconductor Mega Factories
01:10 Micron Technology’s Factory Operations Center
02:39 Silicon Transistors: The Basic Units of All Computing
04:34 Taiwan’s Chip Production Facilities
05:47 Micron Technology’s Mega Factory in Taiwan
08:00 Semiconductor Design: Developing the Architecture for Integrated Circuits
08:45 Micron’s Dustless Fabrication Facility
11:06 Wafer Processing With Photolithography
13:13 Automation Optimizes Deliver Efficiency
14:50 Monitoring Machines from the Remote Operations Center
16:37 Transforming Chips Into Usable Components
18:41 Mitigating the Environmental Effects of Chip Production
21:40 A World of Ceaseless Innovation
22:30 End Credits
How TSMC Became Taiwan’s Silicon Shield? https://youtu.be/-i7U53miOeo
#Micron #TSMC #Semiconductor #Taiwan #MegaFactories #TaiwanPlus #Microchips #Microchip
▁▁▁▁▁▁▁▁▁▁▁▁▁▁▁▁▁▁▁▁▁▁▁▁
🌏 TaiwanPlus | Taiwan to the World
Breaking news and original programs. All things Taiwan at your fingertips.
Visit our website » https://www.taiwanplus.com
📱 Connect with TaiwanPlus
» Like us on Facebook: https://tw.plus/facebook
» Tweet us on Twitter: https://twitter.com/taiwanplusshows
» Follow us on Instagram: https://tw.plus/instagram
🇹🇼 About TaiwanPlus
TaiwanPlus is the premier international media platform providing English-language news and entertainment from Taiwan, at the heart of the most dynamic and fastest growing region on Earth.
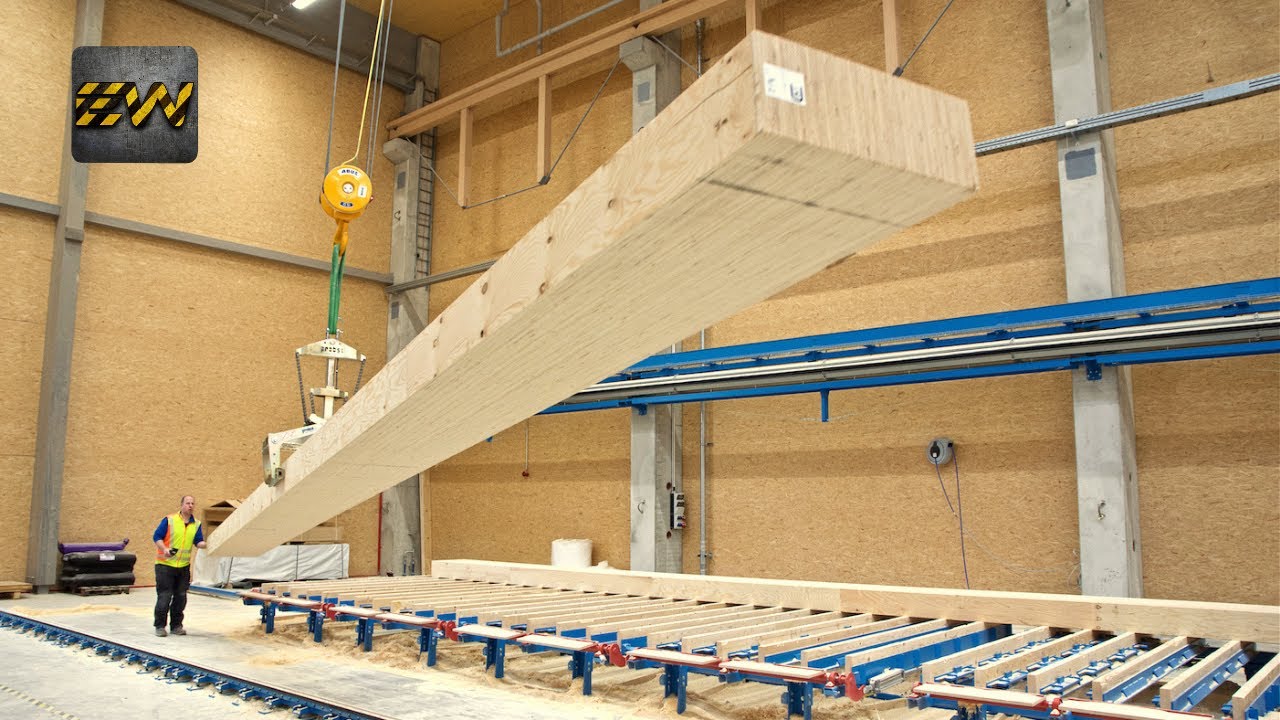
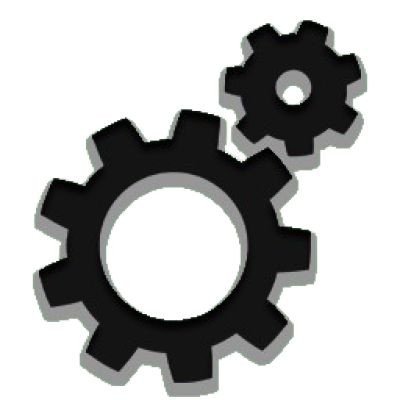
Plywood production requires a good log, called a peeler, which is generally straighter and larger in diameter than one required for processing into dimensioned lumber by a sawmill. The log is laid horizontally and rotated about its long axis while a long blade is pressed into it, causing a thin layer of wood to peel off (much as a continuous sheet of paper from a roll). An adjustable nosebar, which may be solid or a roller, is pressed against the log during rotation, to create a "gap" for veneer to pass through between the knife and the nosebar. The nosebar partly compresses the wood as it is peeled; it controls vibration of the peeling knife; and assists in keeping the veneer being peeled to an accurate thickness. In this way the log is peeled into sheets of veneer, which are then cut to the desired oversize dimensions, to allow it to shrink (depending on wood species) when dried. The sheets are then patched, graded, glued together and then baked in a press at a temperature of at least 140 °C (284 °F), and at a pressure of up to 1.9 MPa (280 psi) (but more commonly 200 psi) to form the plywood panel. The panel can then be patched, have minor surface defects such as splits or small knot holes filled, re-sized, sanded or otherwise refinished, depending on the market for which it is intended.
Plywood for indoor use generally uses the less expensive urea-formaldehyde glue, which has limited water resistance, while outdoor and marine-grade plywood are designed to withstand moisture, and use a water-resistant phenol-formaldehyde glue to prevent delamination and to retain strength in high humidity.
Video Credit: www.westfraser.com
Join 'Engineering World' like many others to get access to special perks:
https://www.youtube.com/channe....l/UCh2wZoBynUkHmTX2G
Also, kindly consider subscribing to our channel if you liked the video: https://geni.us/SubscribeChannel
Watch some of our other interesting manufacturing videos:
How Cement Is Made?
https://youtu.be/RcrMBYsB93E
How LUXURY Rolls-Royce Cars Are Made ?
https://youtu.be/BVvnSzMqI3M
How Jigsaw Puzzles Are Made?
https://youtu.be/nylElsB9MkE
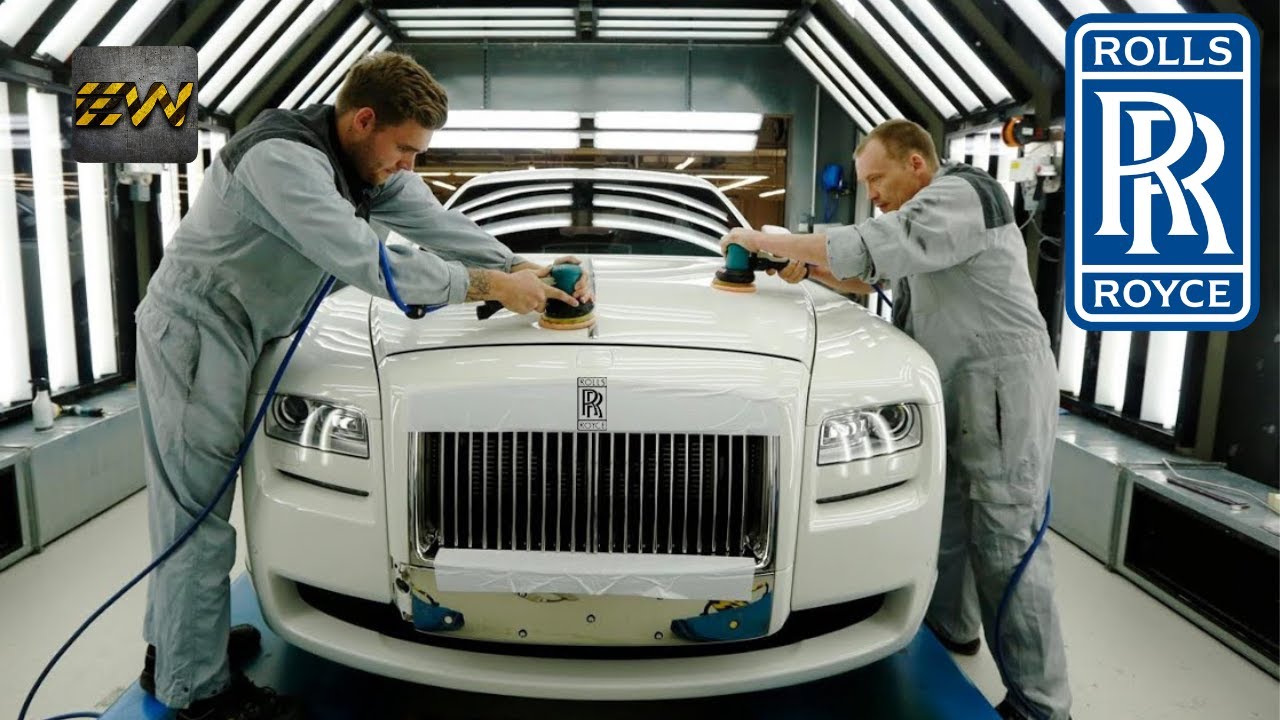
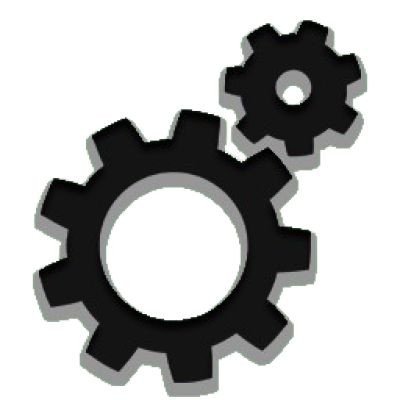
Rolls-Royce Motor Cars Limited is a British luxury automobile maker. A wholly owned subsidiary of German group BMW, it was established in 1998 after BMW was licensed the rights to the Rolls-Royce brand name and logo from Rolls-Royce plc and acquired the rights to the Spirit of Ecstasy and Rolls-Royce grill shape trademarks from Volkswagen AG. Rolls-Royce Motor Cars Limited operates from purpose-built administrative and production facilities opened in 2003 across from the historic Goodwood Circuit in Goodwood, West Sussex, England, United Kingdom. Rolls-Royce Motors Cars Limited is the exclusive manufacturer of Rolls-Royce branded motor cars since 2003.
Although the Rolls-Royce brand has been in use since 1906, the Rolls-Royce Motor Cars subsidiary of BMW AG has no direct relationship to Rolls-Royce-branded vehicles produced prior to 2003 other than being a major engine and other supplier prior to 2003. The Bentley Motors Limited subsidiary of Volkswagen AG is the direct successor to Rolls-Royce Motors and various other predecessor entities that produced Rolls-Royce and Bentley branded cars between the foundation of each company and 2003, when the BMW-controlled entity started producing cars under the Rolls-Royce brand
Video Credit: www.rolls-roycemotorcars.com
This video is part of our ‘How Everyday Things are Made’ series. To watch other video of the series click on this link: https://youtube.com/playlist?l....ist=PLmHzFWJOOSAoI1i
Join 'Engineering World' like many others to get access to very special perks:
https://www.youtube.com/channe....l/UCh2wZoBynUkHmTX2G
Also, kindly consider subscribing to our channel if you liked the video: https://geni.us/SubscribeChannel
Watch some of our other interesting manufacturing videos:
How Plywood Is Made In Factories?
https://youtu.be/3Wh9NYvfStk
How Engines are made?
https://youtu.be/SH_unRLBRw4
How Jigsaw Puzzles Are Made?
https://youtu.be/nylElsB9MkE

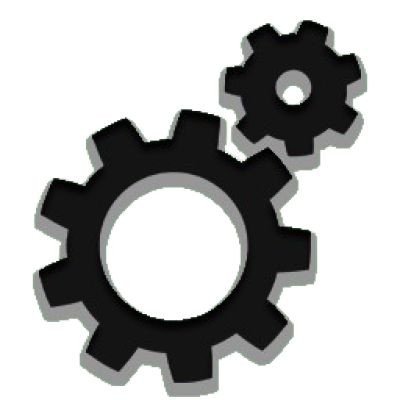
Mega Manufacturing: Airbus A350 | 4K Engineering Documentary
Build your own Airbus A350: https://amzn.to/3LVjh2F
World's Most Advanced Supercars: Birth of the Automobile: https://youtu.be/LbD8leFCB-I
Assembled in France using millions of components made throughout Europe: The A350 is the most modern commercial aircraft in the world.
The Airbus A 350: the most modern commercial aircraft in the world. It takes 1800 highly-skilled specialists in Toulouse, France, and 2.5 million individual parts, delivered from all over the world, to assemble this masterpiece of aeronautic engineering. The goal: An aircraft with minimal consumption and maximum range. 53 percent of the Aircraft consist of a modern ultra-light composite material. But the innovative material also requires entirely new manufacturing processes. A challenge for the aircraft manufacturers in Toulouse. And the final assembly is preceded by a logistical masterpiece: The individual parts of the aircraft travel from various Airbus plants in Europe to Toulouse: the front and centre sections from Saint-Nazaire in France, the tail section from Hamburg, the wings from Broughton in Wales and Bremen, and the tail fin from Getafe in Spain. The factory in Toulouse is supplied with these parts by a specially developed transport aircraft, the Beluga. Several times a day, five of these machines commute between the various plants and bring supplies for production seven days a week from early in the morning until midnight. And the journey of the components is not over in Toulouse. By the time the A350 is fully assembled it will have passed through seven hangars or "stations." Given the extremely high number of components that have to be assembled and the large number of different suppliers, there are a lot of risk factors involved in the production of the A350. And the pressure is high: The modern aircraft is extremely popular with airlines, with 890 pending orders to date. Ten aircraft of the A350 have to leave the factory every month no matter what.
▬▬▬▬▬▬▬▬▬
Subscribe Free Documentary Channel for free: https://bit.ly/2YJ4XzQ
Facebook: https://bit.ly/2QfRxbG
Twitter: https://bit.ly/2QlwRiI
▬▬▬▬▬▬▬▬▬
#FreeDocumentary #Documentary #MegaManufacturing
▬▬▬▬▬▬▬▬▬
Free Documentary is dedicated to bringing high-class documentaries to you on YouTube for free. With the latest camera equipment used by well-known filmmakers working for famous production studios. You will see fascinating shots from the deep seas and up in the air, capturing great stories and pictures from everything our beautiful and interesting planet has to offer.
Enjoy stories about nature, wildlife, culture, people, history and more to come.
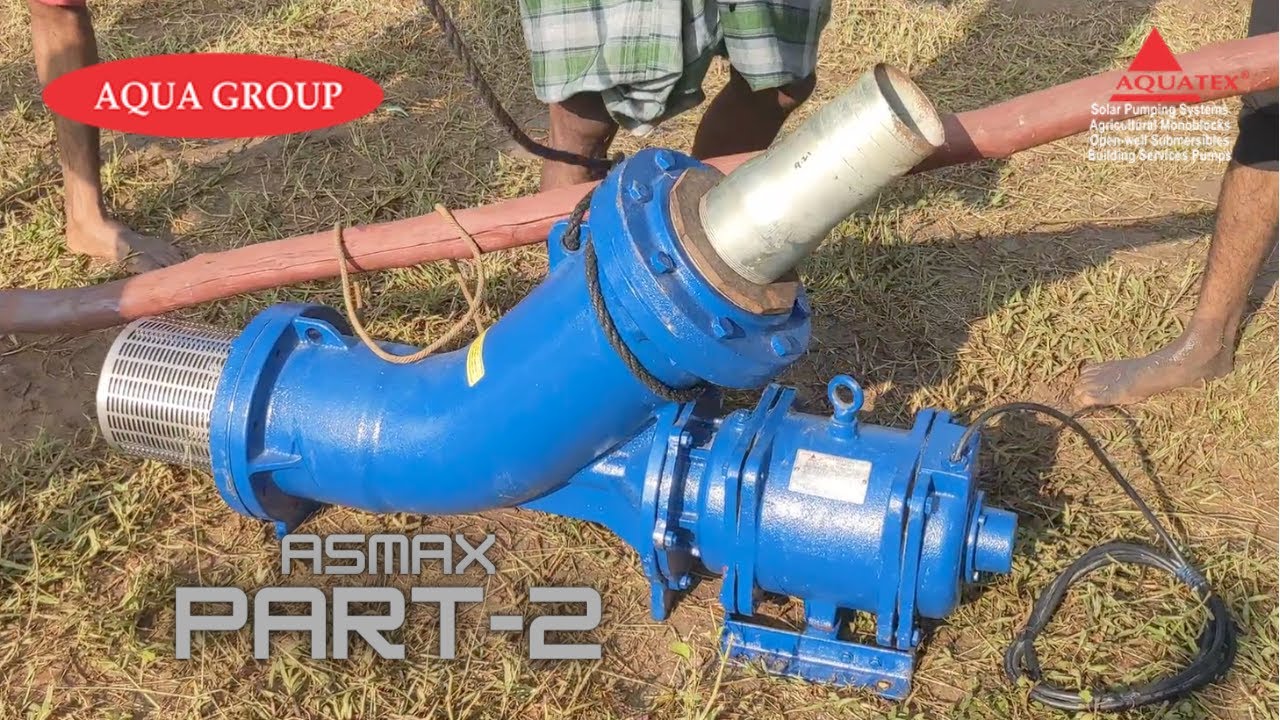
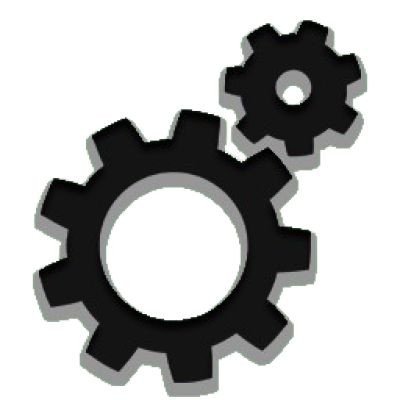
Link to Part-1 video - https://youtu.be/h6IwZ2weabI
AQUAGROUP’S “AQUATEX” OPEN WELL SUBMERSIBLE PUMPSETS offer the convenience of not having to change the position of the pump with changing water levels in the well. They are rugged and efficient, reliable and are built to withstand tough operating conditions like low voltages, etc.
The new ASMAX SERIES horizontal, open-well submersible pumps are commonly used for Low-head, High-discharge applications.
General specs- THREE PHASE OPEN-WELL SUBMERSIBLE MONOBLOCKS, HIGH DISCHARGE, AXIAL FLOW, WATER-COOLED, 380VOLTS, 50HZ, AC POWER SUPPLY.
Variants:
1. ASMAX37150 - 5.0HP(3.7KW)
PIPE SIZE- 150x150 mm
HEAD RANGE- 3.0/6.0 m
DISCHARGE RANGE- 57.0/35.0 lps
2. ASMAX15100 - 2.0HP(1.5KW)
PIPE SIZE- 100x100 mm
HEAD RANGE- 3.0/4.5 m
DISCHARGE RANGE- 22.0/9.0 lps
CONTACT DETAILS:
RAVI ELECTRICALS, DINDIGUL & PALANI
PH: 9944880624
VNJ ENGINEERING, DINDIGUL @VNJ ENGINEERING
PH: 9967410321
Thank you.

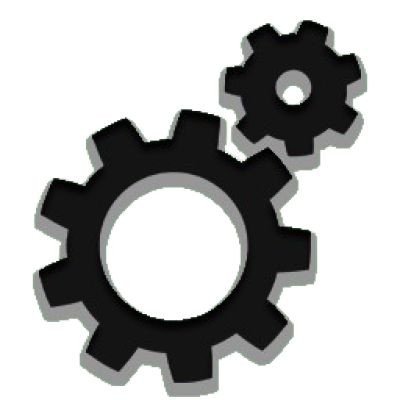
Old But Amazing Manufacturing Process of Car Alloy Rims | Production of Car Alloy Rims
The "Old But Amazing Manufacturing Process of Car Alloy Rims" showcases the timeless techniques used to create durable and lightweight wheels. This process involves the careful selection of materials, emphasizing the historic methods that have been refined over years. In the "Old But Amazing Manufacturing Process of Car Alloy Rims," alloys are meticulously cast, shaped, and treated to ensure the highest quality. Each step, from casting to finishing, in the "Old But Amazing Manufacturing Process of Car Alloy Rims," reflects a blend of traditional craftsmanship and enduring designs. Finally, the "Old But Amazing Manufacturing Process of Car Alloy Rims" culminates in the creation of rims that are not only functional but also embody a piece of automotive history.
===============================================
➤Follow me on Instagram: https://bit.ly/3J8wV1H
➤Follow me on Facebook: https://bit.ly/3MYnvXW
➤Subscribe on YouTube: https://bit.ly/3NmFcl6
➤Email: mechanicalskill84@yahoo.com
===============================================
Related Tags
#OldButAmazing #CarAlloyRims #ManufacturingProcess #ClassicCars #WheelCrafting #AlloyRimRestoration #alloyrims #production #mechanicalskills